When many individuals accidentally spill coffee on their clothing, they typically encounter frustrating stains. However, Alex White and John Mohr viewed this situation as a chance for innovation. They set out on a path where they not only discovered how to create textile ink from coffee grounds but also established a successful business.
When the majority of individuals accidentally spill coffee on their shirts, they typically notice frustrating stains. However, Alex White and John Mohr perceived this as an opportunity. With Mohr's extensive experience as a screen printer for large commercial clients spanning over three decades, he desired to venture into something new. Together with his son-in-law Alex White, they embarked on a journey where they not only discovered how to create textile ink from coffee grounds but also established a thriving business known as Domestic Stencilworks.
The team initially started experimenting with a range of natural pigments such as beet juice, red wine, and even beer. "In the beginning, it was quite straightforward - if an ingredient could stain clothing, we believed it was a suitable candidate for experimentation," White mentioned in an email interview. However, although staining was uncomplicated, the challenge arose when attempting to print with natural pigments on garments and ensuring that the prints endured through wash and wear. "In reality, overcoming this obstacle has taken us nearly three years," White added.
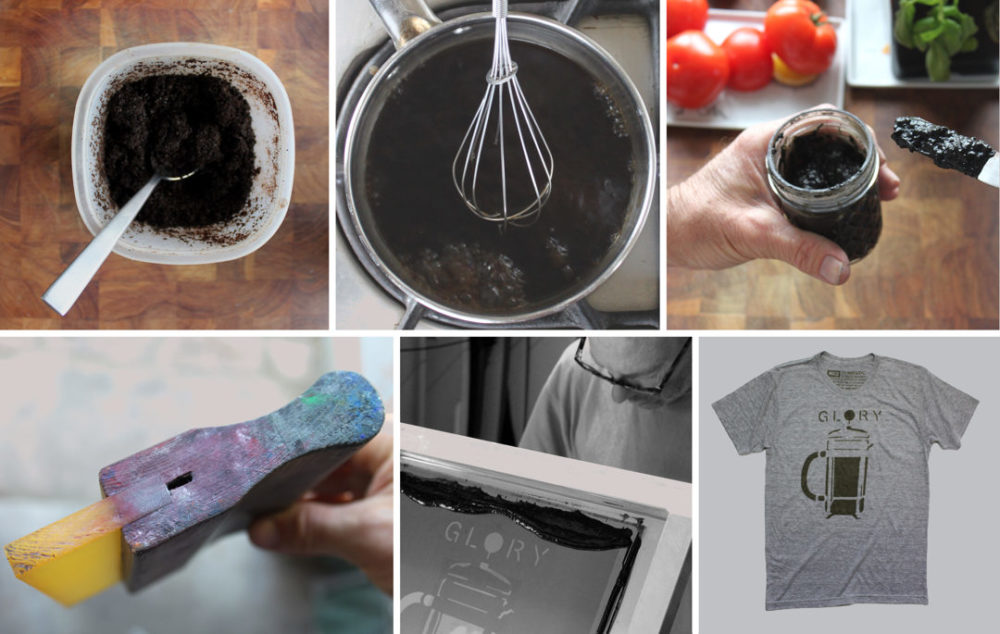
Ultimately, they determined that spent coffee grounds were the perfect ingredient for their screen printing ink. The grounds are combined with vinegar, strained, and then cooked to allow excess liquid to evaporate until the mixture resembles the consistency of screen ink. Once cooled, the ink is prepared for printing. Does it sound straightforward? "There are a few undisclosed secrets that we are keeping to acknowledge the numerous hours it took for us to develop a viable product, but that's essentially the process," Mohr explains.
Mohr has dedicated over 30 years to his craft as a screen printer, but his latest project represents largely uncharted territory for him. "The techniques and ingredients we are using to execute print work are unlike anything I have been involved with or been aware of in my years as a screen printer," he explains. Despite this, his accumulated experience has equipped him with a variety of skills. "Although this approach is brand new, I am able to leverage many of those old trade secrets to our advantage."
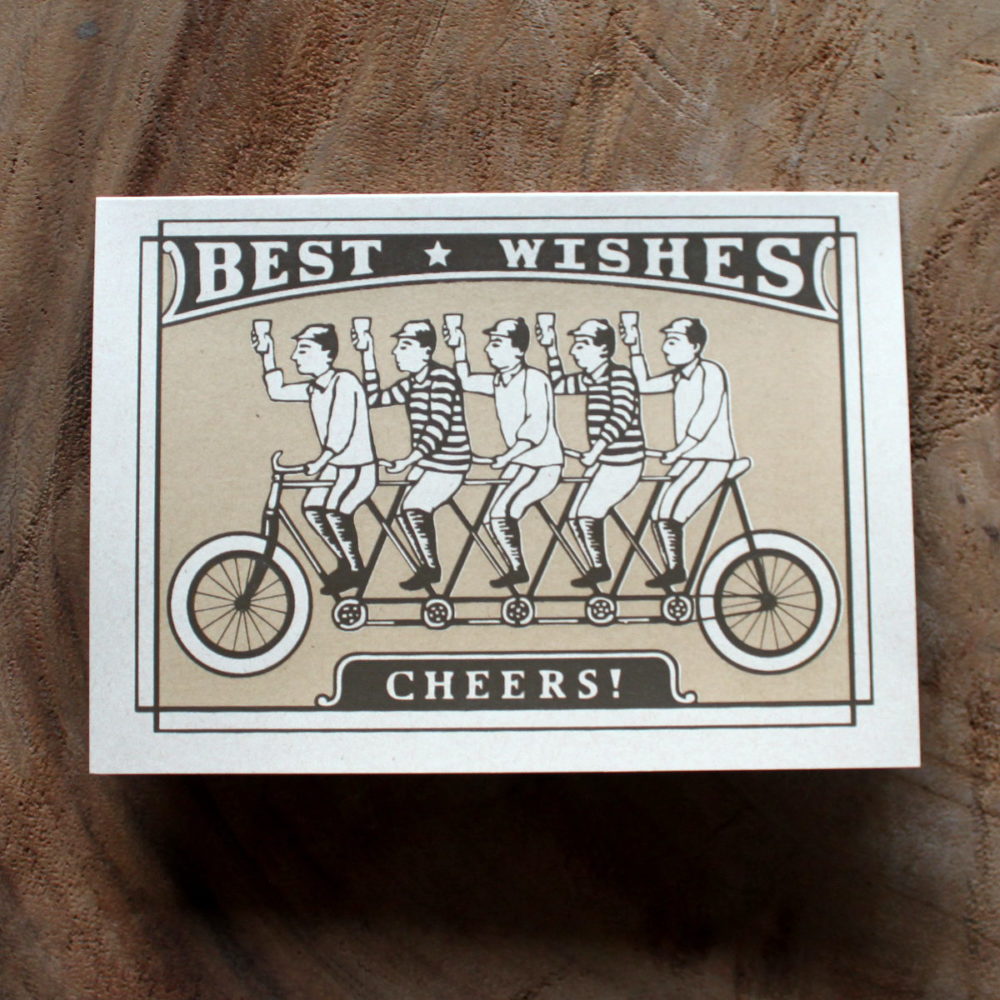
Utilizing ink made from coffee grounds for printing offers several advantages. Firstly, it is cost-effective as high-quality screen inks can be expensive, whereas vinegar is inexpensive and coffee grounds are often readily available at no cost. Additionally, coffee inks are sustainable as the process does not involve the use of chemicals, and the grounds, which are typically considered waste, are repurposed, contributing to a circular economy.
The procedure utilizes only a small quantity of coffee grounds, eliminating the necessity for substantial donations from coffee chains at this time. However, Domestic Stencilworks has introduced a special offer for coffee shops and chains. Alex White explains, "We provide custom dye creation at no extra cost, enabling individuals, shops, roasters, or brands to send us their used grounds. We then utilize these grounds to create the dye for their print run. This allows individuals the chance to enhance their own narrative and inform their supporters that the garments they are buying were made from their product after it had been enjoyed in liquid form."
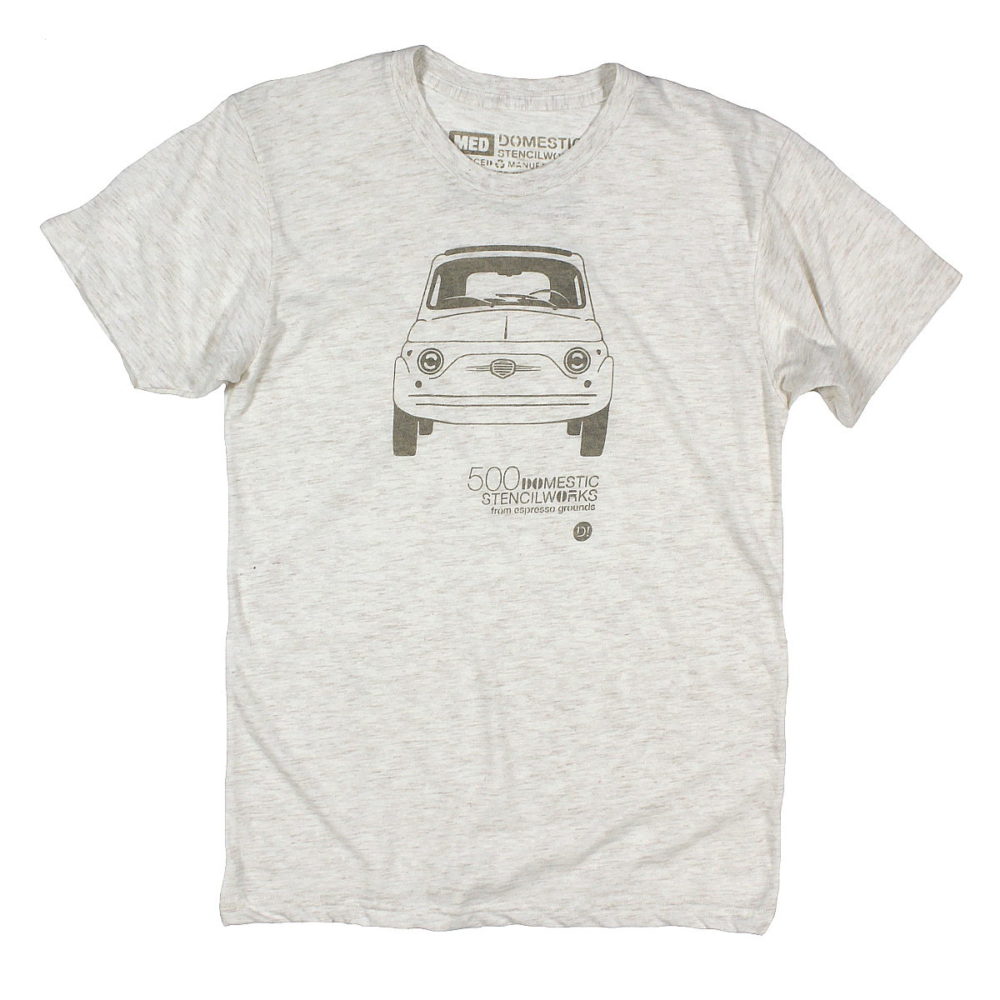
The innovative pair has primarily concentrated on printing t-shirts, but they are planning to broaden their product range. "In addition to garments, our coffee dye prints exceptionally well on paper. We are currently expanding our stationary line to include more pieces that utilize coffee dye," mentions White. On the other hand, Mohr and White are also experimenting with plant-based dyes that have shown success on paper for application on garments. "Mixed greens, carrots, and beets are currently our preferred choices," adds White.
Due to the popularity of the t-shirts, Mohr and White received numerous requests from other screen printers to purchase the coffee ink. However, they have chosen not to sell it at this time. They explain, "Along with creating the dye, there is a very specific technique, order of operations, and curing process that are necessary for it to turn out properly. We would hate to sell a large quantity of ink and have customers be dissatisfied with their results. The prospect of guiding numerous customers through the process seems overwhelming to us."
Mohr and White, who frequently work late nights manually printing t-shirts, have found their journey to be incredibly rewarding thus far. Mohr expresses, "The satisfaction of this endeavor lies in my ability to prioritize quality and craftsmanship in a more artistic setting, rather than a corporate production environment. While we still maintain high production volumes and aim to further increase them, our focus remains on the artistry, which brings me immense joy."